プラスチック部品の未来を握る、IOTによる生産管理
プラスチック成形と組立が主要業務である栄和産業株式会社(小牧市藤島町)。IOT化のきっかけは、ベトナム人技能実習生が増える中、手書きの日報による生産管理がしづらくなってきたことだった。プロジェクトを牽引した管理部部長の宮嶋重光氏が、「この紙ベースの日報作業を、なんとかデジタル化できないか」。そう考えたことで事態が動き出した。
プラスチック製造業界を取り巻く現況に対応
——まず初めに、プラスチック部品の製造業界では、現在どのような構造変化が起きていますか。販売先となる大手自動車・電機メーカーの海外進出に伴い、中堅・中小のプラスチック製品製造業者のアジアの国々への生産移転も進んでいます。また、アジア諸国の低価格品に対抗するため、大量生産が可能な製品は海外生産・加工、国内においては高付加価値製品や精密部品の生産という住み分けが行われているようですが。
宮嶋部長:私たちの主要取引先は、国内大手総合電機メーカーや大手自動車メーカーです。材料不足である現在の社会情勢とも関係しますが、基本的には、IOT化の流れは、モノづくりの合理化の追求から始まっていると思います。各種作業はもちろん、材料の調達などを含むスピード化によって、より顧客さまにご満足いただくことが、自分たちの規模の会社には必要不可欠です。
ご存知のように、安価で大量生産できる商品は、海外生産にシフトしています。そうなると、国内企業には多品種・小ロットの商品が残ります。例えば自動車も、かつては同一車種が多く造られていましたが、現在は多品種となり、その部品も様々です。これらの生産には、やはりコストがかかり、その中でいかにして品質を上げるかということが課題になります。
また、安価だからと、中国や東南アジアの国々に生産をシフトしたことで、日本では半導体関係をはじめ、多くのモノづくりができなくなっており、それは反省すべき点だと言えるでしょう。ただ近年は、少しずつですが、半導体関係の国内生産を再開した会社も見られます。
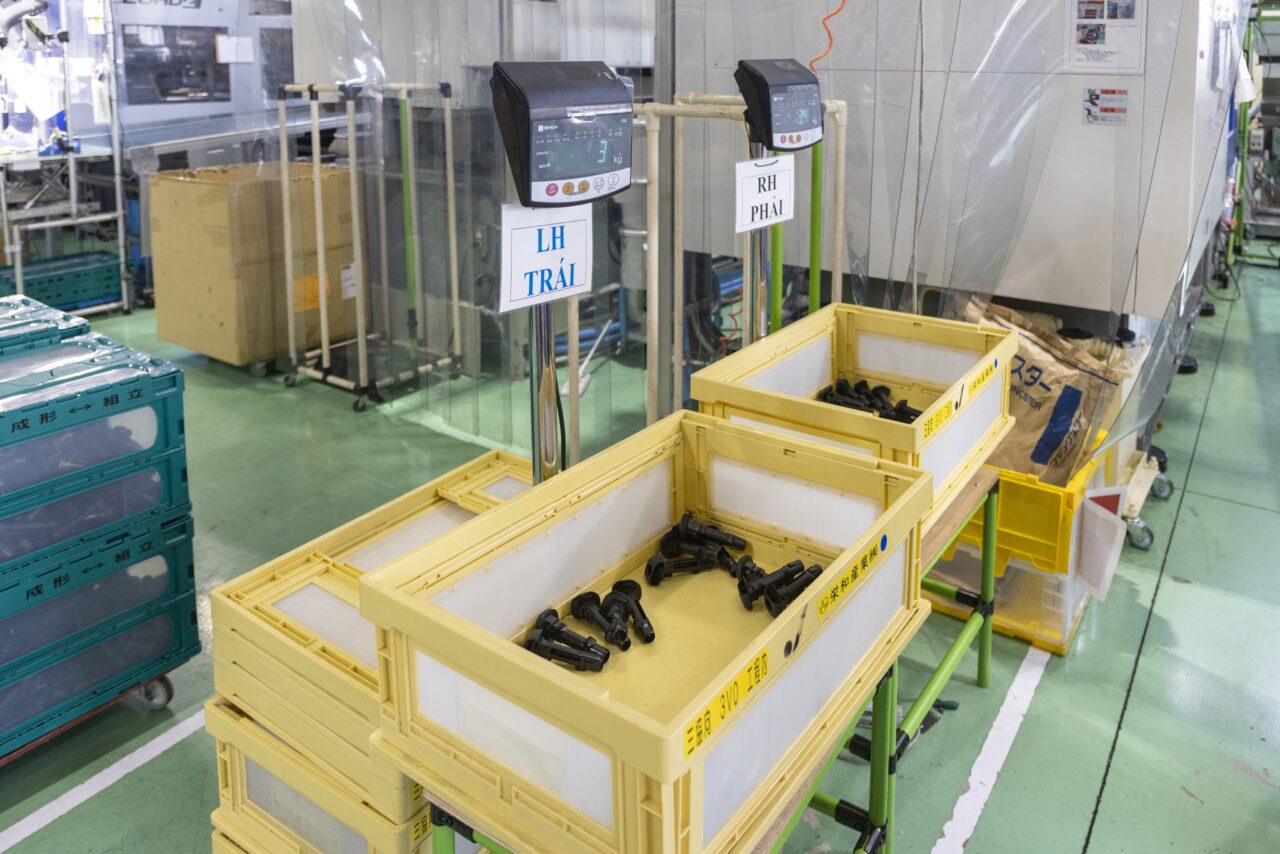
自動車のヘッドレスト内の部品。数の確認は機械が行うが、不良がないかどうかは人の目で検品する
——サビに強く腐敗しない点がメリットであるプラスチックですが、一方で、廃棄後の環境汚染につながるという懸念が強まっています。焼却時に生じる二酸化炭素も地球温暖化の原因となることから、近年では環境に適した素材の利用が求められますが、どのように対応されていますか。
宮嶋部長:プラスチックの見直しは、社会的な動きです。実際の取り組みとしましては、発注元である大手メーカーさんが、「ケナフ」という植物繊維をプラスチックのように使いたいと考えており、すでに私たちの工場でも、その一部の製品を造っています。いずれは、プラスチックの一部がそれらに置き換わっていくのかと思われますが、やはりネックはコストがかかることです。大手メーカーさんでもなかなか広げていけず、留まっているというのが現状です。しかし、こういった取り組みが実を結び、土や環境に還る素材が主流になる動きが出てくるのではと思い、対応したいと考えています。
また、当社としては、産業廃棄物になるような不良品は造らないようにすることが、環境への取り組みの一つだと考えます。もう一つは、不良品が出た時に粉砕してペレット化し、再利用の樹脂を使う仕組みを作っていることです。これは、お客さんと相談して認めていただいた場合に限りますが、技術的にも今は2〜3割の再生率というところ。これらをまず、半分の5割くらいに上げていきたいですね。そうすれば、プラスチックは再生可能な素材となっていくのではないでしょうか。
——これらの時流を踏まえ、今回のIOT導入やシステム化との関連は。
時流として、IOT化は必要ですから、かねてから取り組みたいと考えていました。しかし、最初はきっかけが掴めずにいました。実は、私は定年まで長野県にあるグループ会社(信菱電機株式会社)で働き、20年前に当時の生産管理システムを導入し、効果を見出せたという経験がありました。
現代のシステムであれば、さらなる効果が望めると考え、模索しました。「システムの制作・運営会社を紹介しようか」と、一宮市にある友人の会社から言われたこともありましたが、その友人の会社自体がまだIOTを導入していない状態。2020年頃で、周囲では、部分的にIOTを導入している会社があっても、トータル的に導入した会社は見つからないという時期でした。そこで、「モデルケースがないなら、まずうちが模索しながら挑戦してみよう」と考えました。
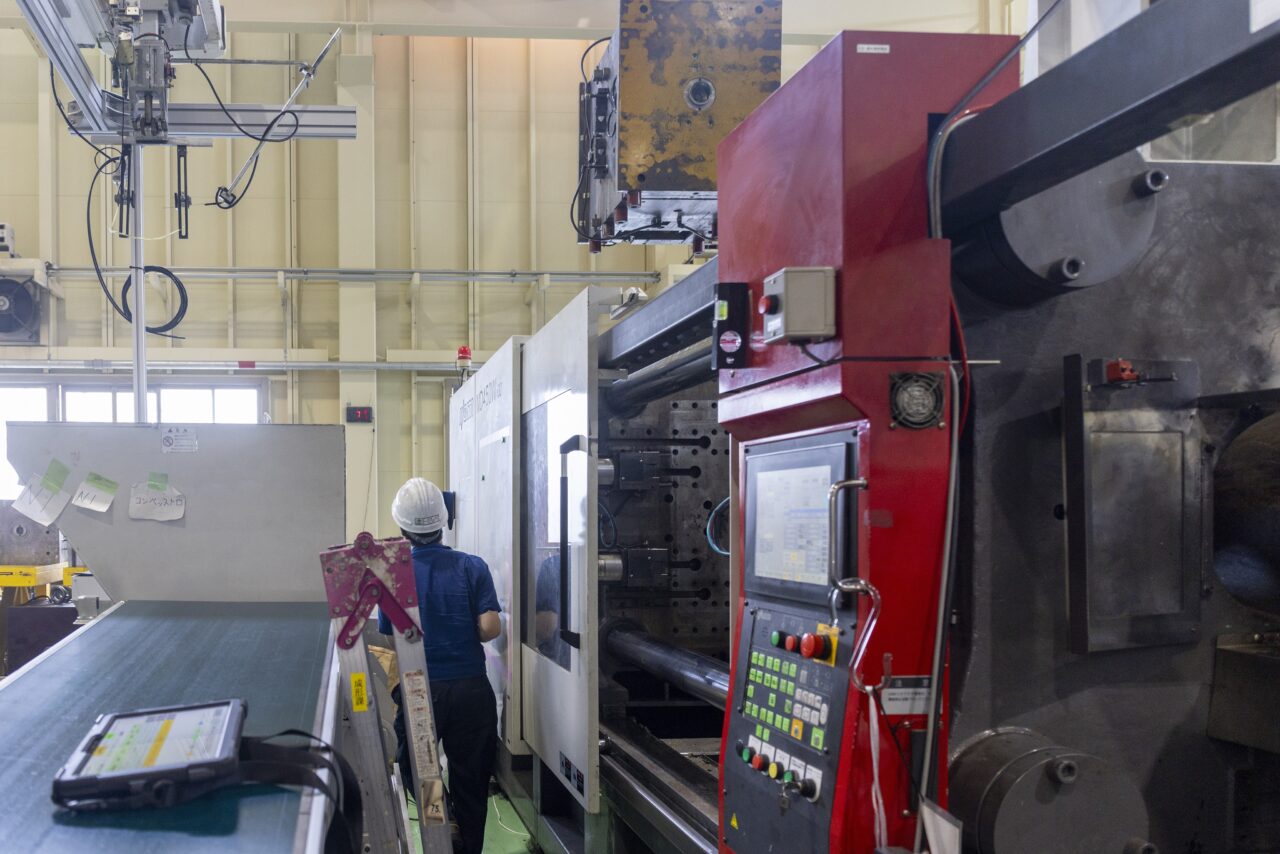
こちらは制御盤を作る作業場。ベルトコンベアー上にあるのは段取りをする作業者のタブレット
ワークショップへの参加を経て、IOT導入への意識が変化
今回のIOT導入のメインには、宮嶋部長と、業務部システム課システムグループ兼総務課の川手翔太さんの2名が指名された。川手さんは川手孝浩代表取締役の息子で、ウェブ系企業に勤めたのち、栄和産業株式会社へ。入社10日後からIOT導入の立ち上げを担った。
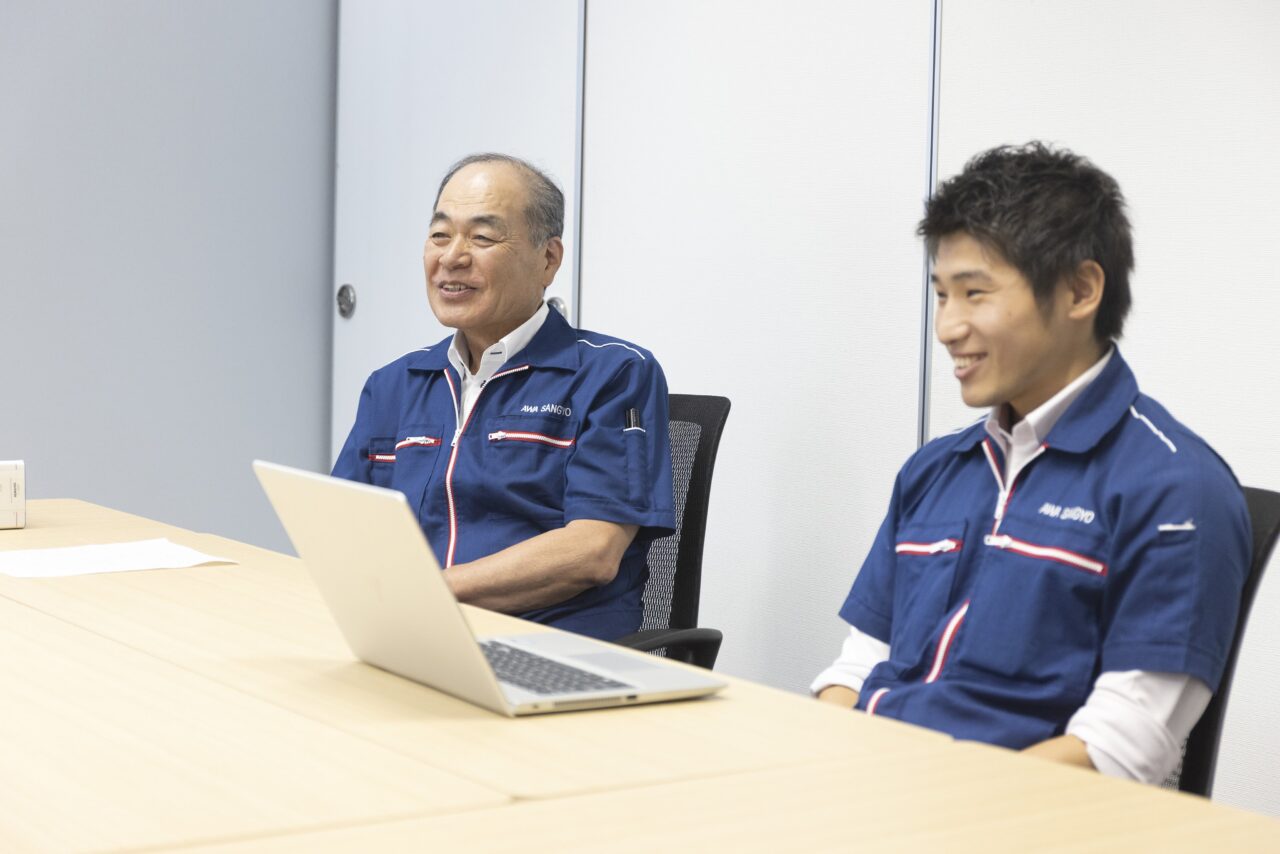
ともにIOT導入の指揮をとった、宮嶋重光部長と川手翔太さん
——IOT導入に関係する、製造現場の具体的な課題は。現場で指揮をとった川手さんも交えてお伺いします。
川手さん:まず1つ目の課題は、30人が在籍する成形の部署において、作業中の実績が見えにくいことです。紙ベースで不良品情報は把握していましたが、どこまで正確かがわからない状態でした。2つ目の課題は、日報やデータ集計が手作業で行われていたことです。30人のうち25人がベトナム人と、技能実習生の割合が増える中で、日報の書き方から教えなければならない状況になっていました。そこで、まずは誰でもわかるようにデータを「見える化」しようと考えたのです。
早速、社長と宮嶋部長から従業員へ、「IOTを始めたい」と伝えましたが、みんなは「IOTとはなんぞや?」という状態。そこで2021年に、『こまき新産業振興センター』さんへ研修に行くことにして、ワークショップに参加しました。最初はシンプルに「日報だけシステム化しよう」という話でしたが、私の中で「果たしてそれをIOTと呼べるのか」という疑問が残りました。そして、ワークショップの中でIOTを実践する他の工場を見学させていただき、方向性が変化しました。ある工場のラインに、センサーを付けて出来高を集計するというワークショップを体験したことで、「自社でも、成形機から実際のデータを取り込みたい」と考えたからです。
宮嶋部長:IOTを取り入れるにあたり、私が重要だと思うのは、「ルールが大事」ということです。川手さんはシステムのことに詳しいものの、入社して間もないので、仕事内容のことはあまりわかりませんでした。例えば日報の付け方にしても、これまでは生産が終わった時に、それぞれが機械を止めていました。でも、実際は「1000台の区切りで止めたい」という人もいれば、「材料がもったいないからここまで打ってしまおう」という人もいたので、比較するデータにばらつきがありました。そこで私が主導して、生産数を統一するなどのルールを、その都度設けていきました。
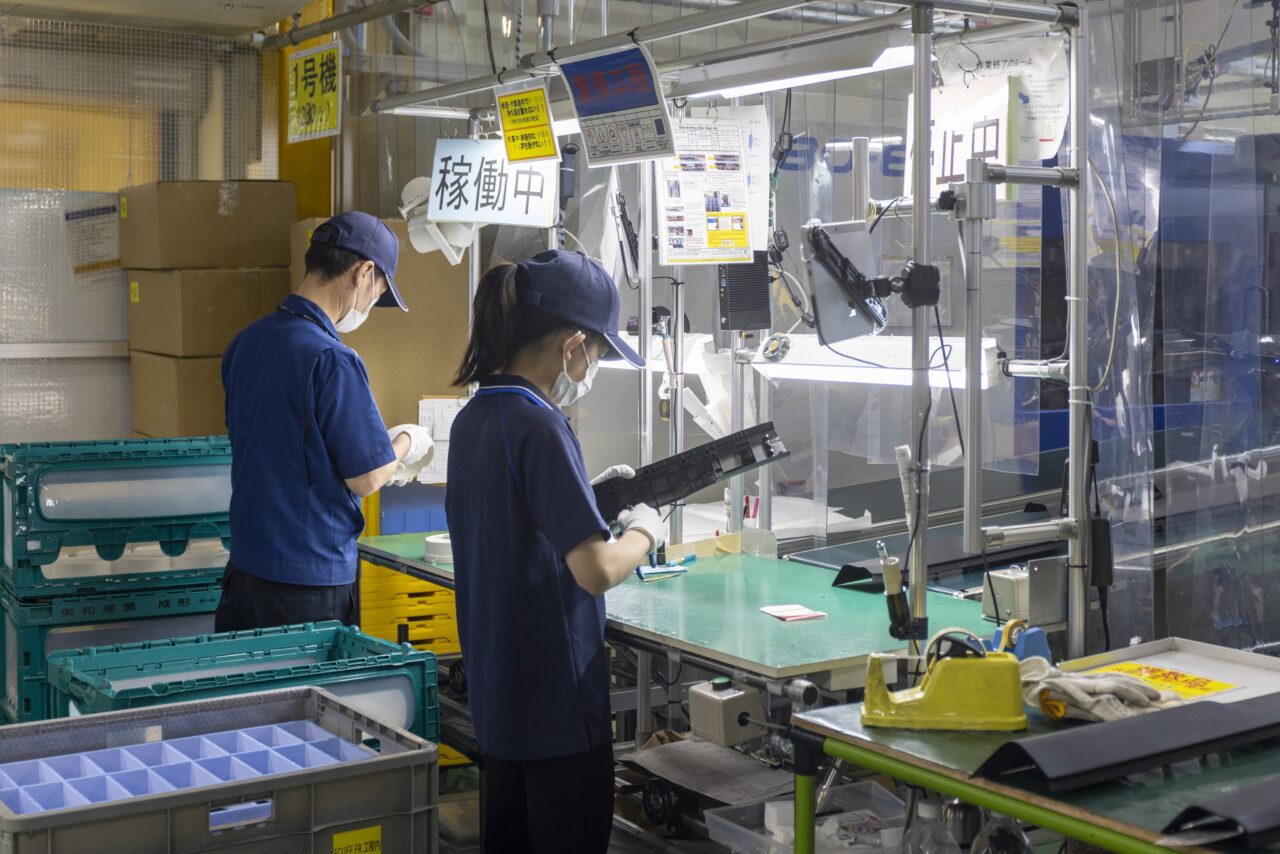
自動車関係のプラスチック部品を製造中。ベトナム人技能実習生のタブレット画面はベトナム語で表示されている
成形で第一の問題である「不良品をいかに減らすか」にIOTが貢献
——2022年1月頃からシステムが本格始動。導入効果は、それぞれの立場の方にとってどのようなものでしたか。
川手さん:以前から社長は、「月ごとの成績が見たい」と話していました。ですからIOTによって、前月に比べて生産性が上がったかどうか、不良品の有無などが正確にわかることが好評です。「見える化」によって、時間にもゆとりが生まれるように感じます。
現場では、「日報を手書きするより、明らかに作業がラクになった」と、多くの従業員が感じています。作業中に何か不具合があったら、ボタンを選んで上司に知らせるだけなので、作業に集中することができるようになりました。万が一作業中に不良品が出てしまっても、手を止めて記入するのではなく、画面上で原因を選んでタッチするだけで、原因や作業実績がデータ化されるので、確認する側にも便利です。
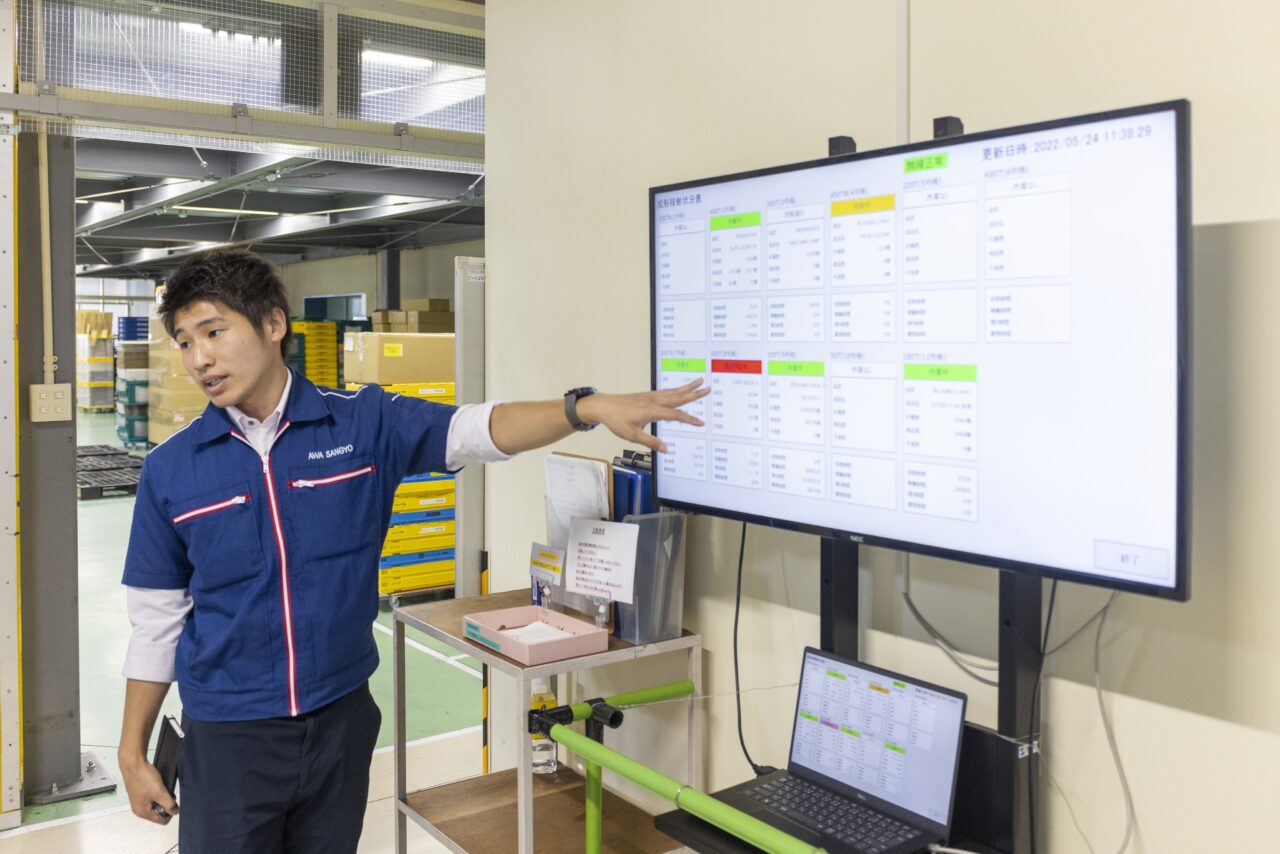
工場の入口にある大型モニターは、「成形稼働状況表」の画面が1分単位で切り替わる。以前は午前と午後に、ホワイトボードに手描きしていたが、今はいつでも状況が一目瞭然
また、全体の進捗がタイムリーにわかるので、段取りがしやすくなりました。どこかがマスター(計画)より遅れ、それが長引いているようであれば、リーダーがすぐに確認にいきます。現場の手が離せないようであれば、事務所にいる係長らが把握して駆けつけます。
往来の手書きの日報と違い、従業員や時間区分ベースで改善が行えるのも良い点です。
今までは成形機毎の手書き日報をベースに改善活動をしていましたのでアバウトな改善しかできませんでした。しかし、生産実績をデータ化することで「誰が」「いくつ」「どの時間に」という情報を正確に把握できるようになり、ピンポイントでの改善ができるようになりました。例えば、作業者にも教育のレベルがあり、入社1日の人と入社1年の人では熟練度が違います。同じレベル、同じ時間帯で比較して不良品を多く出している人がいれば、その人に集中して教育し直すことができます。IOT化によって、技術の標準化ができると思います。
——システム導入後、製品・生産数・納期などの具体的な変化はありましたか。
宮嶋部長:試行錯誤を繰り返し、従業員の教育面に時間がかかったため、まだ本格稼働してから半年ほどですが、変化を感じています。導入当初は、作業者がログインし忘れて、データが取れないことなどもあったからです。精度が上がってからは、製品の不良率でいうと、出やすいものでは10%くらい出ていた不良が、約3%に減りました。これはIOT導入の「見える化」によって、金型改善をしたからです。生産性もすでに1〜2%上がっています。
初期投資は費用と時間、人材が必要
——IOTの機械やシステム導入にあたり、どのような初期投資が必要ですか。
宮嶋部長:まず生産情報を集めるだけなど、シンプルに始めようと思えば、500万円くらいでしょうか。ただ、「IOT化」と言えるほどの初期投資であれば、やはり1千万円から2千万円ほどの費用と、導入作業にかかる時間を見込んでおいたほうがいいと思います。
また、システム制作会社選びも重要です。依頼するシステム制作会社が、成形であれば成形のことなど、作業内容をどれだけ熟知しているかで、やり直しなどの作業量が違ってくるため、費用も変わります。意思疎通ができていたつもりでも、現場で運用してみると、やはり不具合が出てきます。追加作業が増えると費用がかさみますから、ベースの段階でどれだけ使えるものを作ってもらえるかが、費用を抑えるポイントだと思います。
私たちは、先述した友人の会社の紹介で、一宮市のシステム制作会社さんに依頼しました。「パッケージ商品ではなく、まずは小規模で始めたい」というこちらの希望を汲んで動いてくれ、一緒にプログラム内容を作り上げることができて良かったと思います。
川手さん:IOT化にあたり、プログラムのことと仕事の流れの両方がわかる人材も必要です。より正確なプログラムを作ってもらうため、現場とシステム制作会社さんとのパイプ役が欠かせません。自分は入社して間もなかったので、プログラムのことはわかりましたが、成形の作業の流れについては詳しくなく、相当勉強をしてからIOT導入に臨みました。
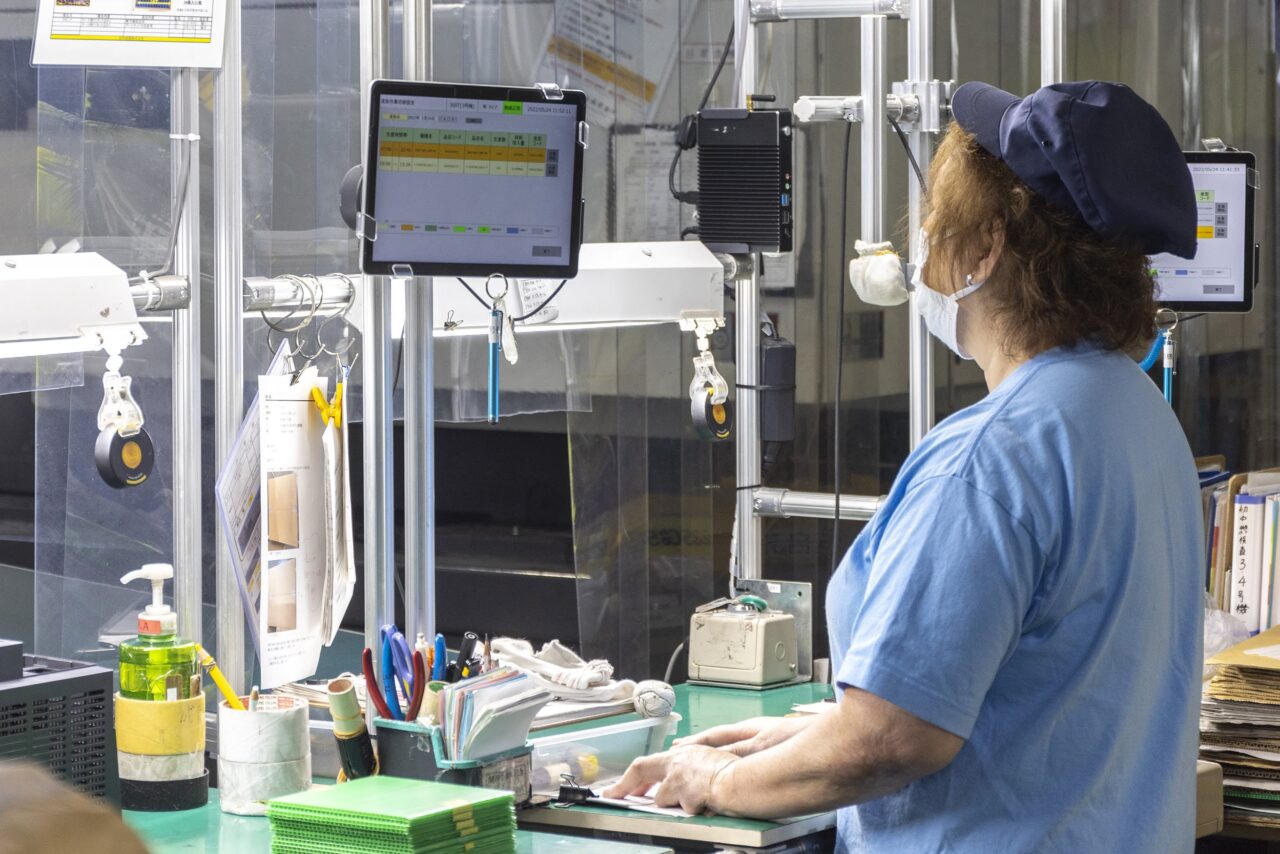
手袋をすることもある作業者。「指ではタブレット画面にタッチがしにくい」という現場からの声を受けて、画面にタッチペンをぶら下げている
——工場内の機械やシステムの配置で、難しかったところや工夫されたところは。
宮嶋部長:製品の異常信号であるパトライトに反応するセンサーが、工場内の日光を拾ってしまうことがあるとわかり、覆いを被せました。また、製品のサイズなどによって、ある位置まで動かさなければセンサーが反応しないということがわかり、配置を工夫しました。こういったことは、実際に現場で運用してみないとわからないことでした。
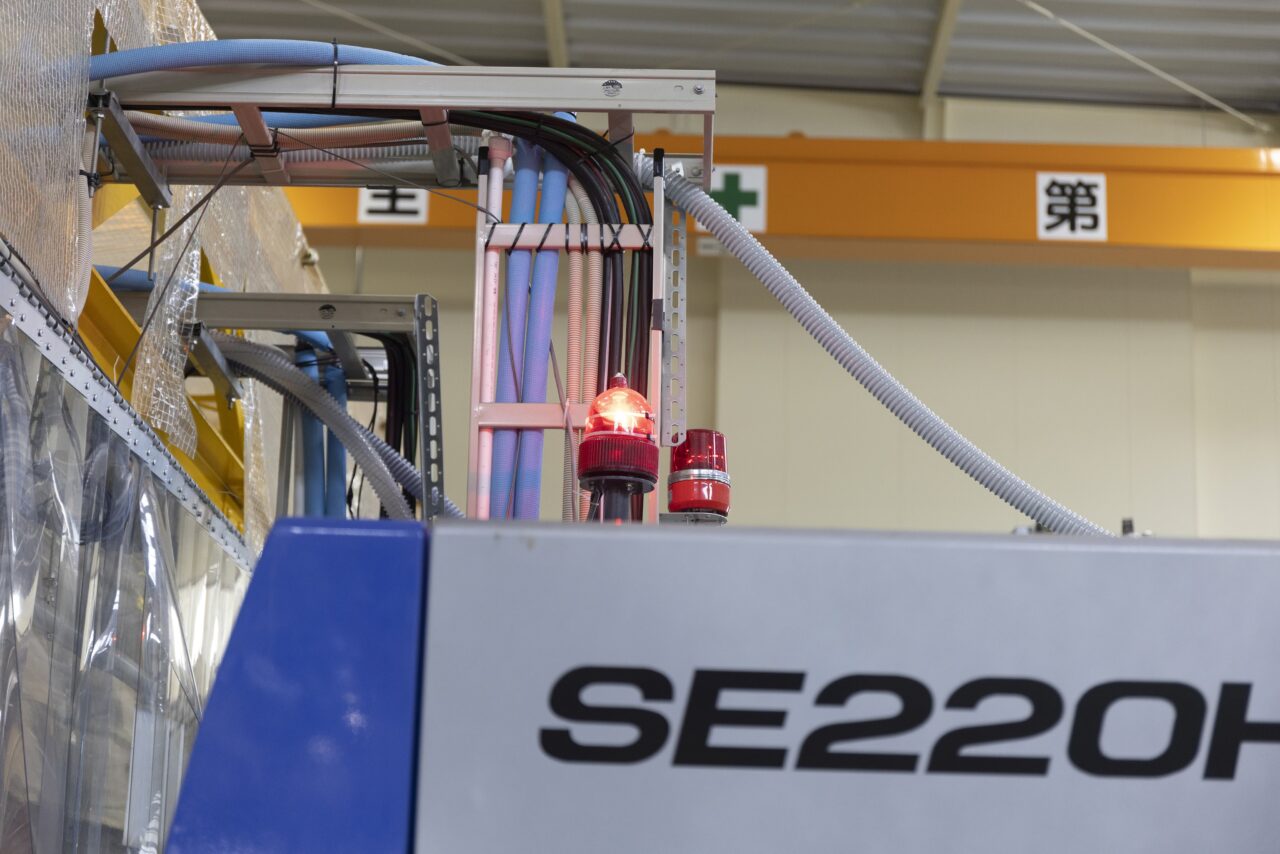
異常を感知した時に点灯するパドライト
信号機は、『こまき新産業振興センター』さんによるワークショップの際、見学させてもらった『松田電機工業所』さんの製品を使用し、配置も見習いました。今後、成形機の変更があってもすぐに対応できるように、センサーを外付けにしたのも、『松田電機工業所』さんを参考にした部分です。データは1つでも欠けると意味がなくなりますが、外付けのセンサーであれば、機械が稼働した状態のままでも設置が可能です。これは後々のコスト削減につながると思います。
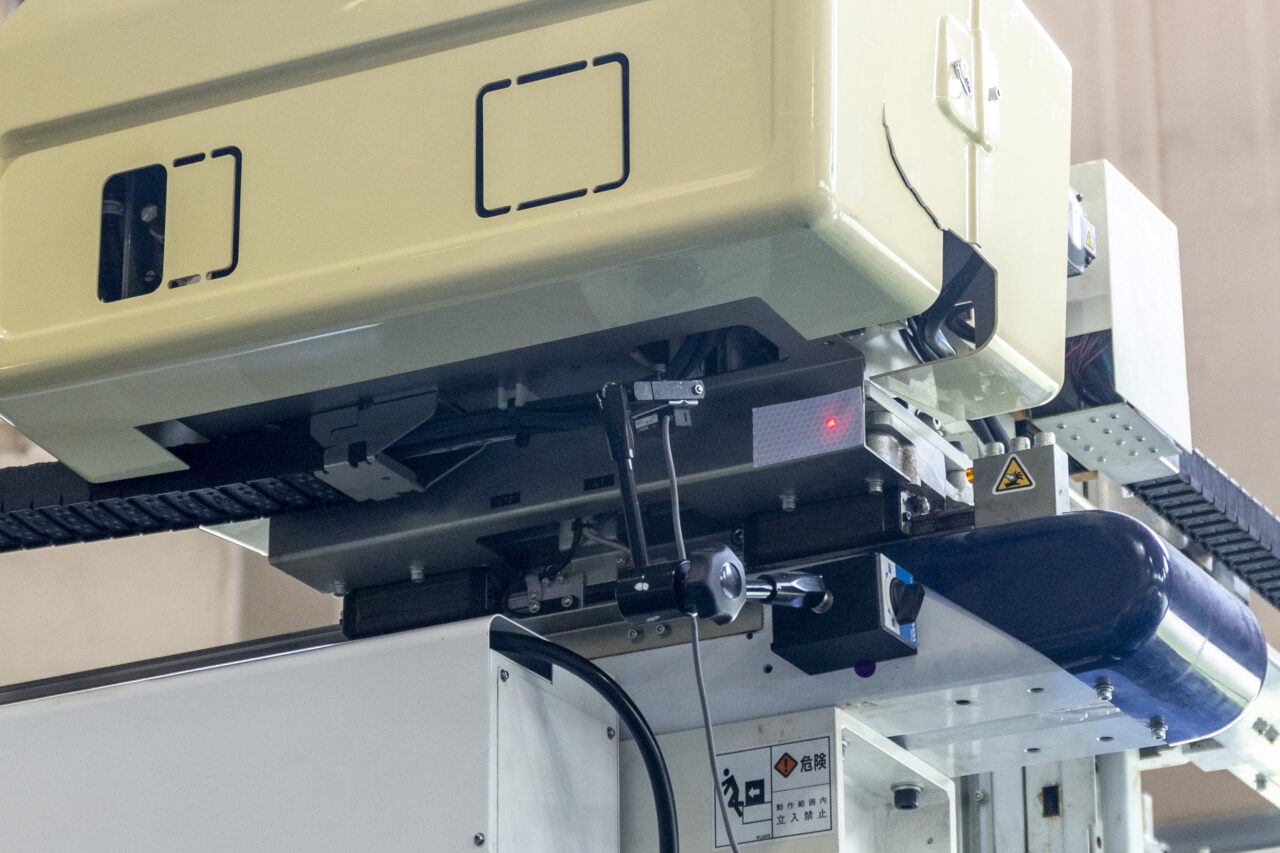
「松田電機工業所」によるセンサー。様々な機械に応用が可能
川手さん:また当初は、タブレットを作業者全員に配るか、リーダーだけが持つかなども検討しました。集中する作業者が、うっかりタブレットを落としてしまうのはという心配もありましたが、一旦、作業者の近くに1台ずつ配置し、作業と入力のしやすさを最優先することにしました。異常により機械を止めることが一番のロスなので、それを未然に防ぐために、ベストな状態にしようと考えた結果です。今のところ、タブレットを落とした例はありませんし、リーダーもずっと全員の画面を見続けているわけにはいかないので、1人1台にして良かったと思っています。
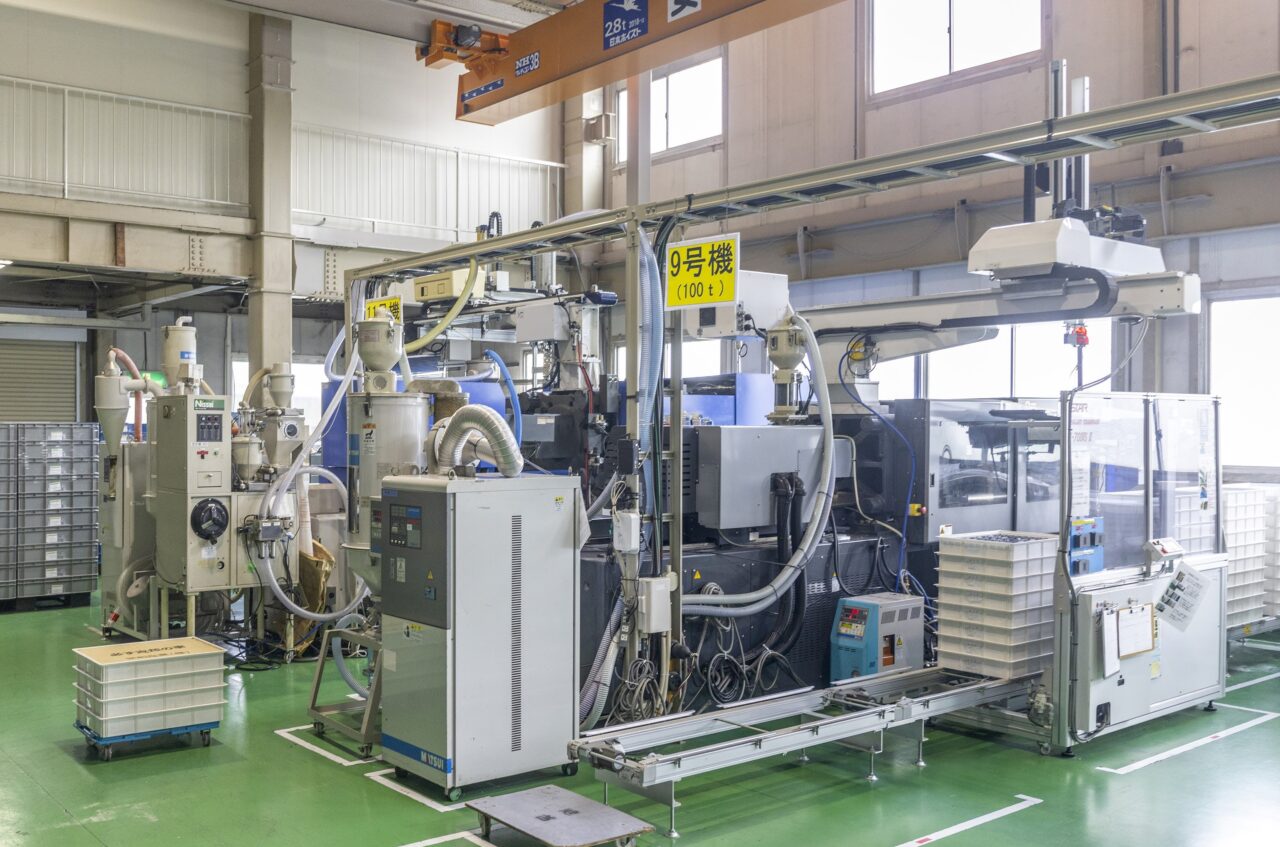
9号機から11号機までの3機は完全に自動化され、24時間稼働。データを区切って集計するベストなタイミングを模索した
——IOT導入にあたり、懸念していたことは。また、それは解消されましたか。
川手さん:やはり、作業者の皆さんに使いこなせるのか?教育面はどうすればいいか?ということを懸念していました。そこで導入前に、IOTに関する勉強会を開きました。また、みなさんが作業しやすいよう、システムに入れる言語は日本語だけにせず、ベトナム語と中国語も加えました。結果的には、皆さん対応してくれています。また、IOTによって、個々の作業情報が追えるようになったので、以前よりも、個人的な教育やフォローがしやすくなりました。その人の良いデータを取り出して褒めることもあります。せっかくのシステムでも、作業者の皆さんに使ってもらわないと意味がないので、これからも工夫していきたいと思います。
自社製品の製造・開発にIOTの力を生かしていく
——今後、品質改善のためのシステム化や自動化について、どのような分野で考えていますか。
宮嶋部長:IOTを組立関係に活用していきたいと考えています。成形に関しては98%活用できていますが、全体で考えるとまだ半分くらいです。次は組立の生産順位について、プログラムの受発注システムと繋ぎながら、何をどの順番で作っていったらいいのかという生産情報を、IOTを使って導きたいと思います。成形でのIOTの経験や反省を生かして、2023年の春頃には稼働したいと思い、先日キックオフしたところです。
また、現在は自社製品の開発に注力し、電気機器部品と自動車関係部品に続く3本目の柱と考えています。部品の製造だけでは、いずれ行き詰まりますから、完成品を造ることが重要です。中でも、介護機器の開発と製造に力を入れており、寝たきりの方に向けた自動排泄処理機「シルバー」を開発中です。寝たきりの方の排泄物を、センサーで感知し、自動で吸引、洗浄、乾燥まで行う機器で、介護の現場をサポートします。こちらは今秋完成予定で、すでに県内の介護施設で実際に使っていただき、テスト段階に入りました1台60万円ほどしますが、介護保険を利用してのリースなどで、施設からの需要も見込んでいます。
環境のことを考えて、この自動排泄処理機が消費者にとって不要になった際は、当社で引き上げ、洗浄、再生、最終的に廃棄するまでを担いたいと考えています。
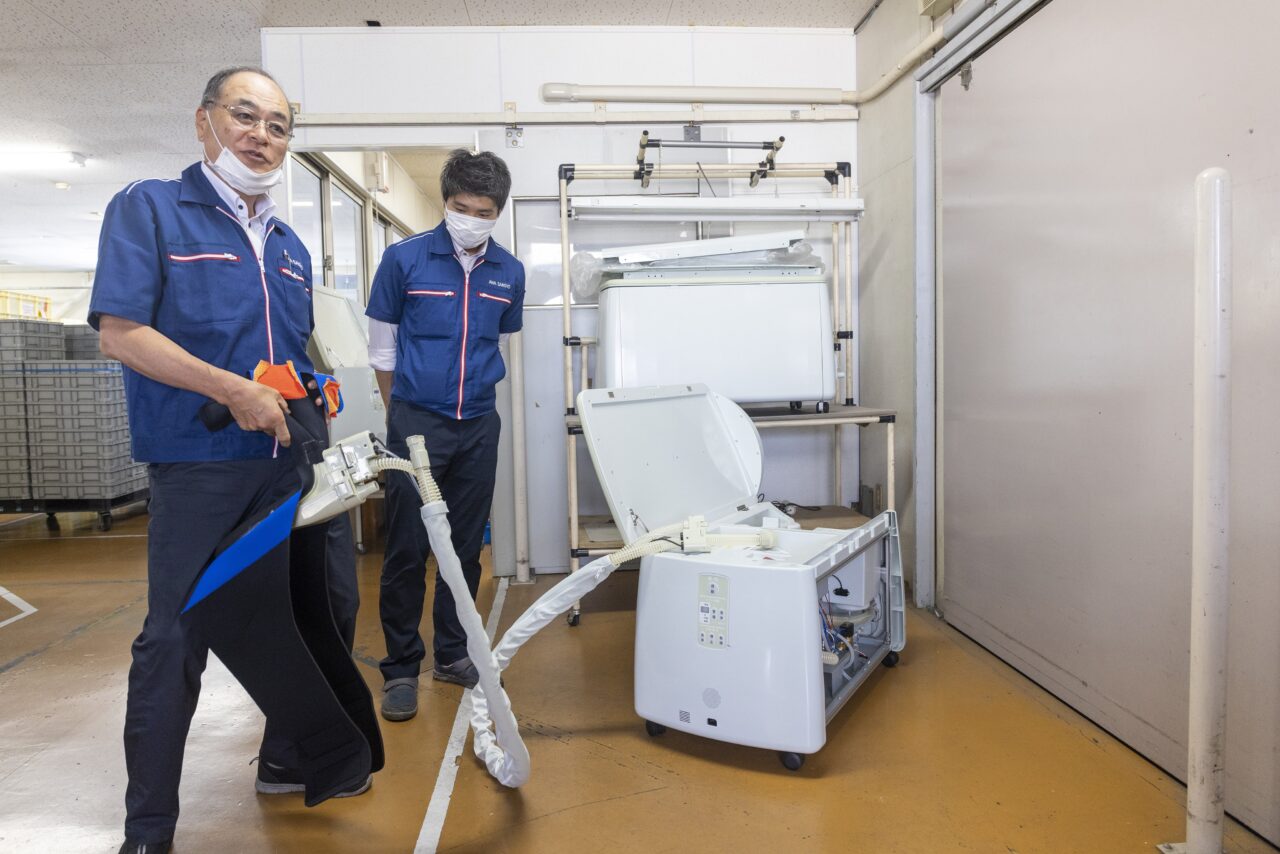
デリケートかつ重労働でもある介護現場の排泄介助に一石を投じる自動排泄処理機「シルバー」
ほかにも、近年は投てき型消火用具や、スプレー式の簡易消火用具、次亜塩素酸水超微粒子を噴霧する、空間除菌システム「ジアグリーンコフレ」などを開発しました。新しいものが好きでアイデアが豊富な社長が、社内公募や、世の中のニーズを読み取って考案する製品が多いですね。
IOTの力を成形や組立に生かすことで、こうした自社製品の開発・製造にも、より力を入れていきたいと思っています。
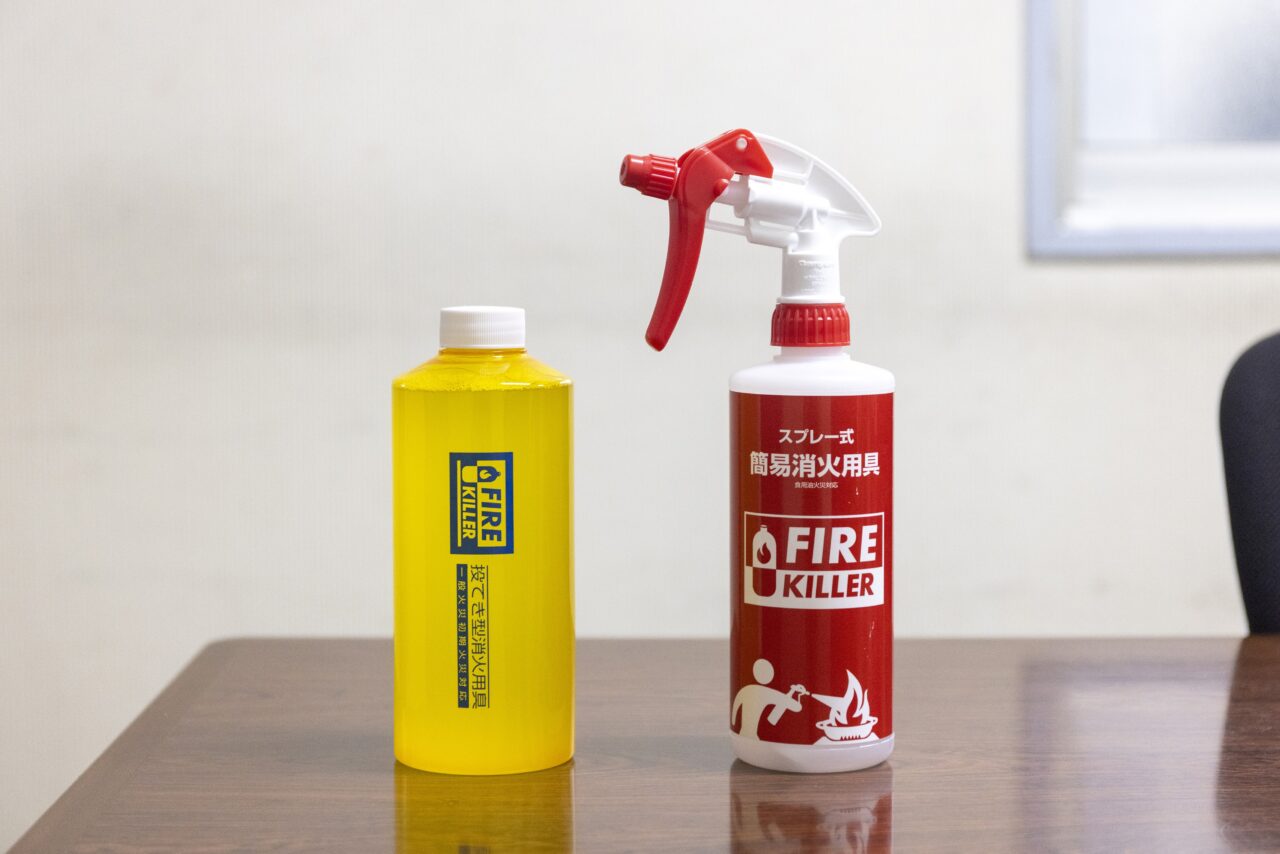
自社製品「FIRE KILLER」。左が投てき型消火用具(定価約7,200円)、右がスプレー式簡易消火用具(定価約7,500円)。投てき型の容器は、衝撃で割れる特殊なプラスチックを使用。建設現場などで重宝されている。スプレー式は家庭の天ぷら油から火が出た時に
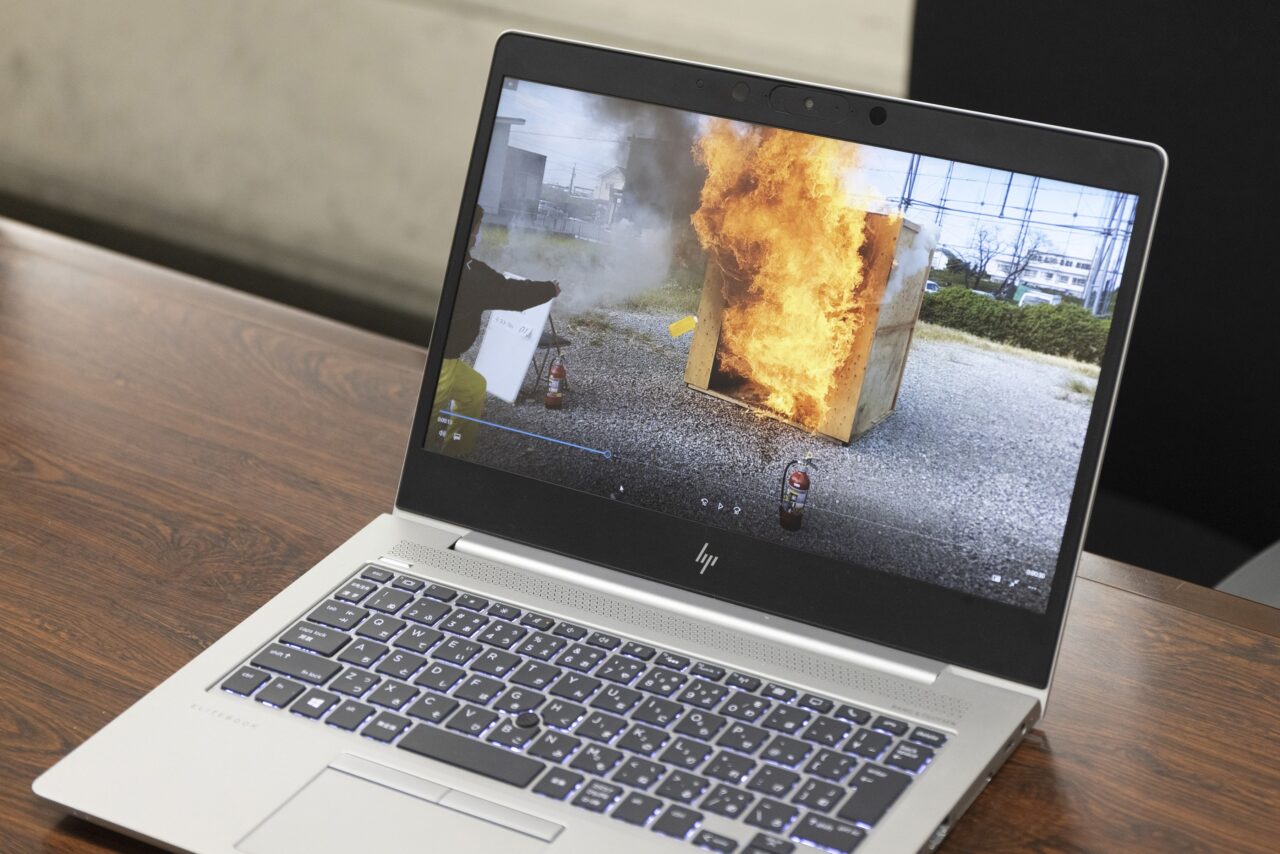
「FIRE KILLER」の高い消火能力は動画でも見られる
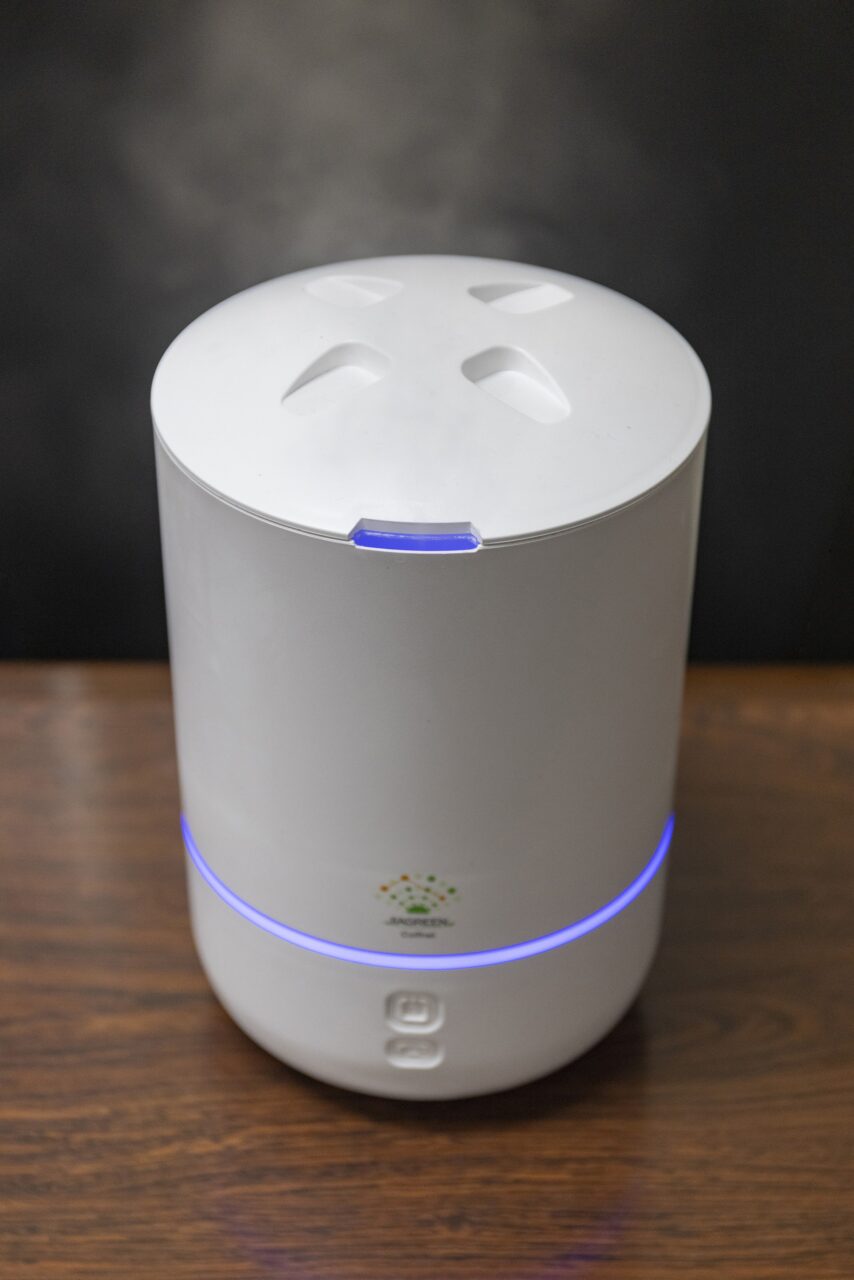
タブレット状の次亜塩素酸を使うことで効果が長持ちする、非電離型微酸性水溶液空間噴霧除菌システム「ジアグリーン コフレ」(定価1万1000円)。コロナ禍以前、インフルエンザ対策に開発した製品が、今また好評
会社所在地
〒485-0061 愛知県小牧市藤島町向江15番地
TEL(0568)73-1102 FAX(0568)73-1103
Webサイト URL
代表者
代表取締役 川手 孝浩
【資本金】
1,000 万円
コメント