ダイキ精工は、ロストワックス製法だけに特化した、全国的に見ても珍しい金型の設計製造会社だ。ロストワックス製法とは、ロウを利用した鋳造方法。まず、加工しやすいロウで製品の原型であるマスターを作り、そのマスターをセラミックで覆ってから、ロウを溶かして焼き固めたものが鋳型になる。そして、できた空洞に溶解金属を流し込み、原型が冷えて固まったら、型を割って製品を取り出して完成となる。
ロストワックス製法に注力する思いを、二人三脚で歩む齋藤宏和代表取締役と齋藤早苗取締役夫妻にお聞きした。
※下記Webサイトリンク
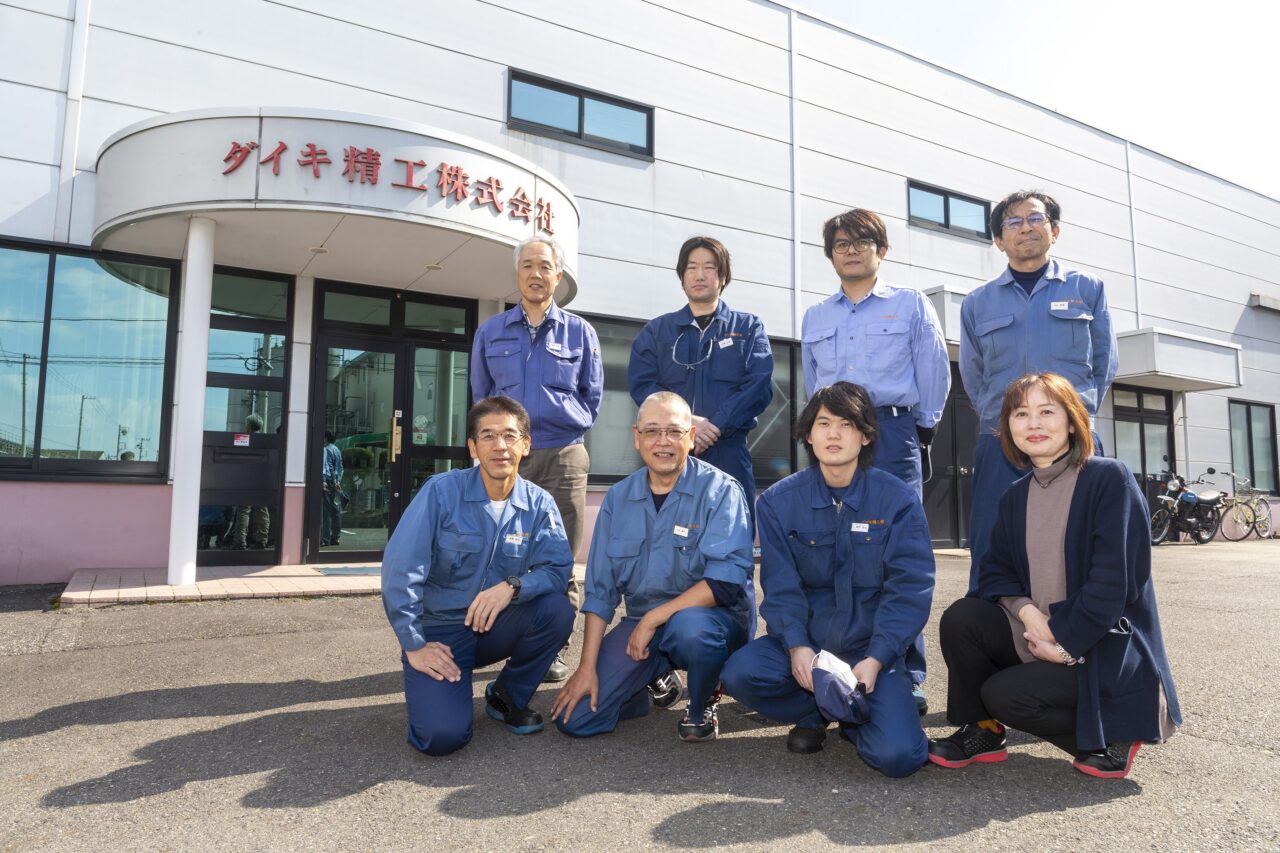
和やかな雰囲気の、ダイキ精工株式会社のメンバー
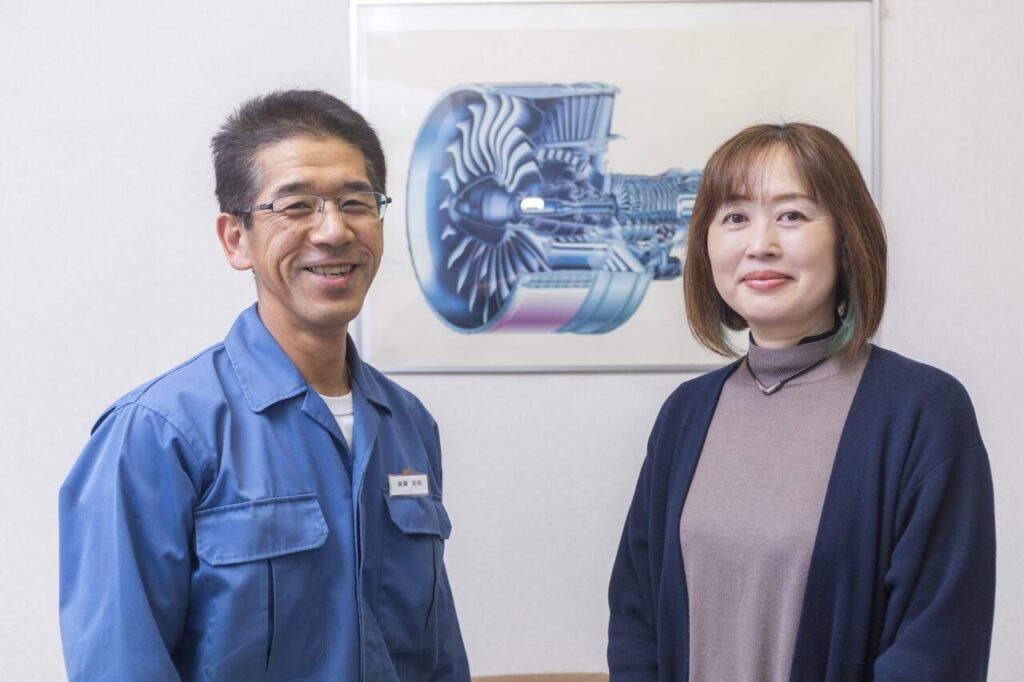
代表取締役の齋藤宏和氏と、総務や経理を経て取締役の齋藤早苗氏
※下記「目次(開く)」バナーから各タイトルをクリックすると、当該記事へ遷移します
複雑な形状の製品を、1/100の精度で製造
製品の材質を選ばず鋳造できることや、複雑な形状の製品の量産にも向いていて、かつ寸法の精度が高く、表面がきれいに仕上がるなどの特徴を持つのがロストワックス製法です。複雑な形状の製品でも一体成型ができるので、溶接の工程をなくせることで、製品の強度も高まります。
この製法の金型だけに特化している企業は、小牧市はもちろん、全国を探しても、珍しいのではないでしょうか。
小さな町工場ですから、自分たちが得意としていることに注力してきた結果、ノウハウの蓄積ができ、お客さまの信頼を得て、この製法に特化していきました。いろいろな業界に進出しても、我々のような小さな会社では勝ち残っていけませんから、今おつきあいをしている企業さんのご依頼に集中していきたいと思っているのです。
製品は、はぐみ(型の見切り面で鋳型が食い違うこと)がないよう、成形機で確認し、100分の1の精度で製造します。
自社の成形機で確認してから納品するため、お客さまは、金型が届いたらすぐに作業に入ることができます。これは、私たちにとって大きなアドバンテージになっています。
ロストワックスの市場は狭く、限られていますから、中国や東南アジアにこの製法を持っていき、簡単な仕事を請け負った業者は淘汰されました。技術の難しさが参入障壁になっているのだと思います。
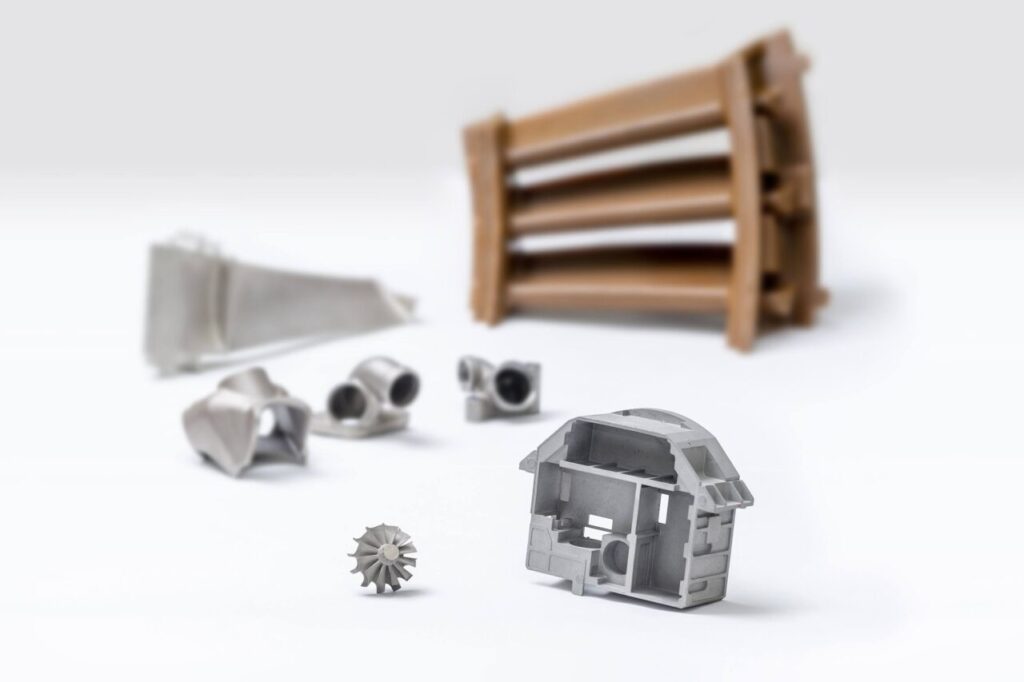
ガスタービンや自動車・飛行機のエンジンの部品たち
製造する製品のメインは、火力発電所のガスタービンの部品や、自動車関係のタービンの部品、航空機のエンジンの部品などです。
ほかにもMRJの主翼の部品の金型も製造しました。
創業当初は簡単な形状の製品から始めましたが、「安価で海外へ発注されるものとは違う、高度で複雑な形状の製品造りにチャレンジしていく」というのが、先代であり現在の会長の大迫喜一郎の考えでした。加工技術の精度に、生き残る術を見出したのでしょう。CADや3Dモデル、5軸マシニングセンタなどの普及で、我々がそれらに挑戦できる環境が整ってきました。
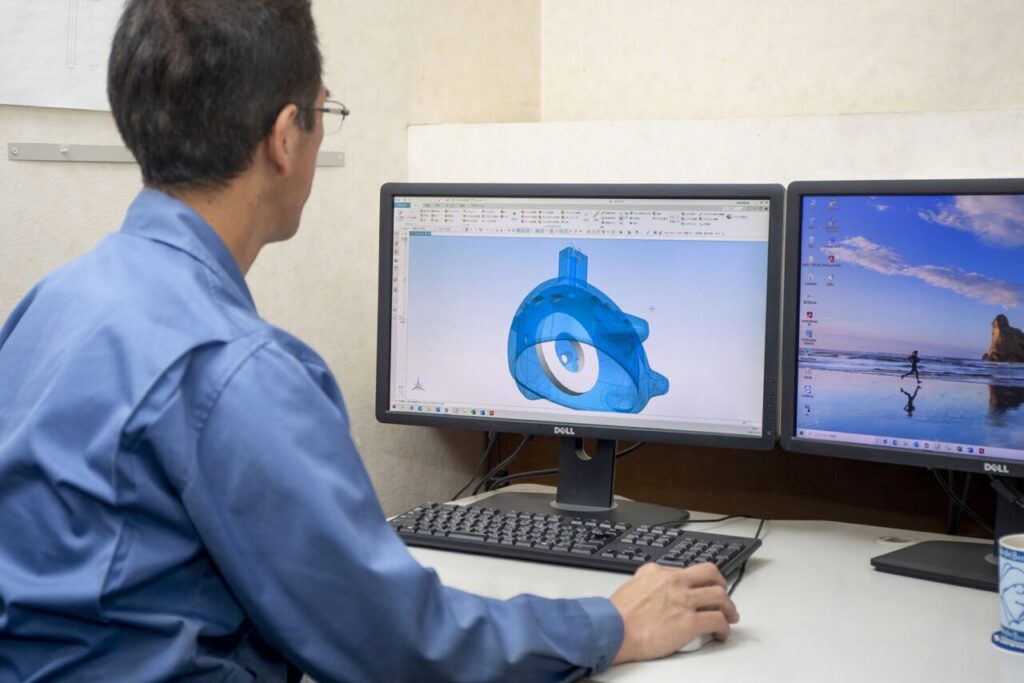
CADを使った3次元での設計の様子
依頼者側の効率や使い勝手を予測して、まだ見ぬ金型をデザイン
顧客からは、製品形状のデータから作って欲しいという依頼を受けます。製品の加工は機械があれば誰でもできますが、製品を「設計、デザインして調整し、まとめる」という作業が大事なのです。自社の話で恐縮ですが、それができる人は少ないと思います。
打ち合わせを重ね、お客さんの工場にある、ワックスを打つ成形機の仕様に合わせて、どの型なら製品が取れるかを把握して、我々がデザインします。
完成品がまだ世にない状況の中で、「これが金型として成立するか」を頭の中で描きながら設計します。最終的に、製品の形を造ることができる金型になればいいので、好きに造ることができるともいえ、設計者によってデザインは全く違いますが、それぞれが「実際に使うお客さんの現場の人たちが、できるだけ少ない工程で、安全に、作業しやすく」と考えて設計しています。ほかにも、素材ごとの収縮度も計算に入れ、「壊れにくく、使い勝手に合わせて設計変更もしやすいように」など、様々なことを含めて設計するのが、うちのノウハウですね。操作性が悪いと、現場の人が段取りなどに時間を取られてしまい、1日に造ることができる製品の個数が少なくなってしまう場合もありますから。
客先の現場の人からも「ダイキ精工さんの金型はとても操作しやすいので、効率よく作業できる」と言っていただけます。やはり、このセンスやデザインの部分で、鋳造メーカーさんからリピートされているのでは、と思います。
その分、金型のデザインは設計者のやりがいでもあり、産みの苦しみもついてきますね。
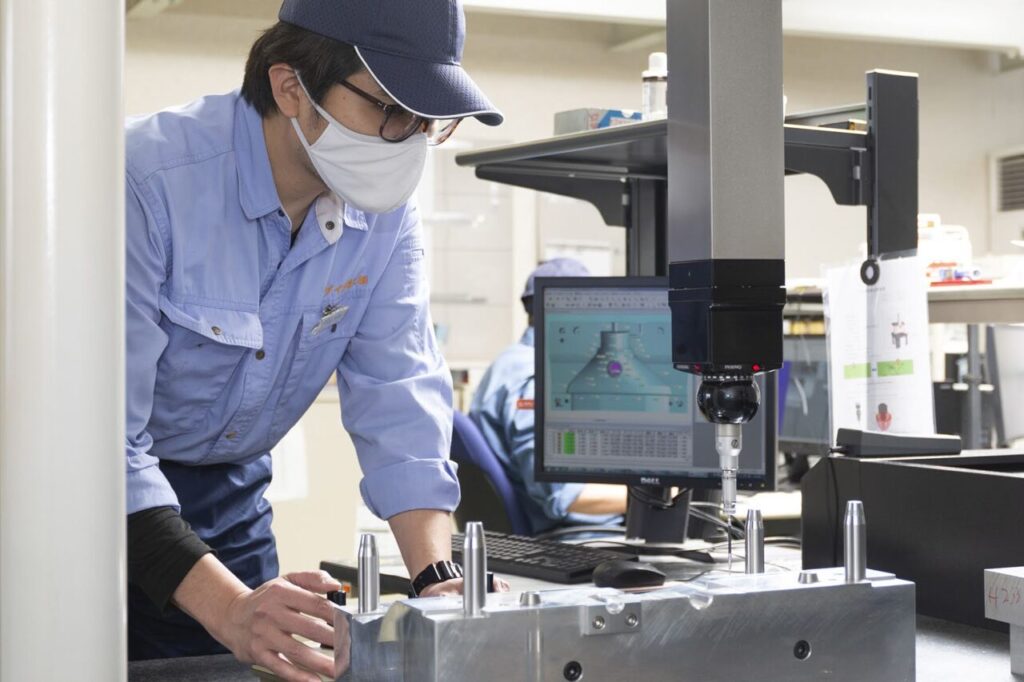
加工した金型の部品を、職人の目で厳しく検査
多くの金属加工業者さんは、図面を見て加工するだけなので、加工した部品がどのように使われるかはわからないと思います。うちは、設計から加工まで携わり、金型にして納めるところまで請け負っているので、部品が組み立てられて金型になる過程がわかっています。すると従業員のみんなも、「この部分は俺が造った!」と実感することができるので、目で見てわかるやりがいにつながっています。
金型の設計者は、加工する人など、作業をする人のことがわかっていないと難しいと思います。私は現場から始めて、現場を知った上で、最終的に設計をするようになりました。従業員の中には、削るのが好きだったり、組み立てるのが好きだったりという人もいて、それぞれが得意なことを活かしながら業務を行っているので、必ずしも皆が設計の道へ進むわけではありません。
従業員の皆さんには、個々の好きなことや得意なことを生かして働いてもらいたいと考えていますが、近年は、好きなことを見つけるまでに辞めてしまう人もいるので残念です。人材育成には時間がかかるもの。難しい仕事ですが、技術を身に付ける長い道のりを、一緒に楽しんでいただきたいですね。
各自を信頼して工程管理を任せ、昼礼時に「可視化」
従業員は60代から20代までの6人です。日々、「何か困っていることはない?」と私から声をかけたり、各自で話したりしてコミュニケーションをとっています。
社内での特徴的な取り組みは、朝礼だけでなく昼礼をしていることでしょうか。昼食後、作業が始まる予鈴の5分前に集まって、現在の進捗状況の報告と、作業内容についての質問を受けます。うちは各自で工程を進められる力量を持った従業員が多いので、細かい部分はそれぞれにおまかせしています。それでも、1つの部品をみんなで作っているため、各自が「次の工程を誰が待っているのか」、「今誰がどのくらいの工数を抱えているか」を昼礼で把握することで、次の工程に早めに入ったり、工数を抱えすぎた人の分を分担したりといった対応に役立てています。ほかの人の工程を可視化することで、「みんなも頑張っているから頑張るぞ!」と、気を引き締める効果もあるのではないでしょうか。
年に一度の親睦会では、みんなで行き先を決めて、協力会社さんも一緒に旅行します。これまでに、海外や広島県、富山県の黒部ダムなどに行きました。また、従業員の家族も呼んで忘年会やバーベキューを開催することもあります。少人数だからこそ、心地よく働いてほしいと思っています。
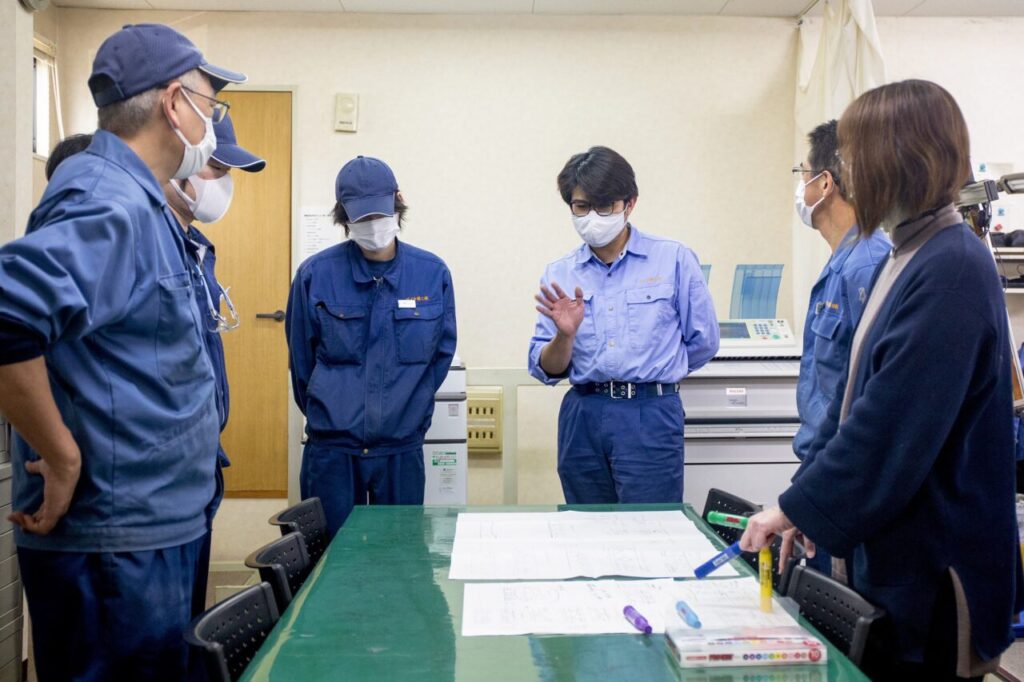
従業員は少数精鋭の6人。潤滑なコミュニケーションが不可欠
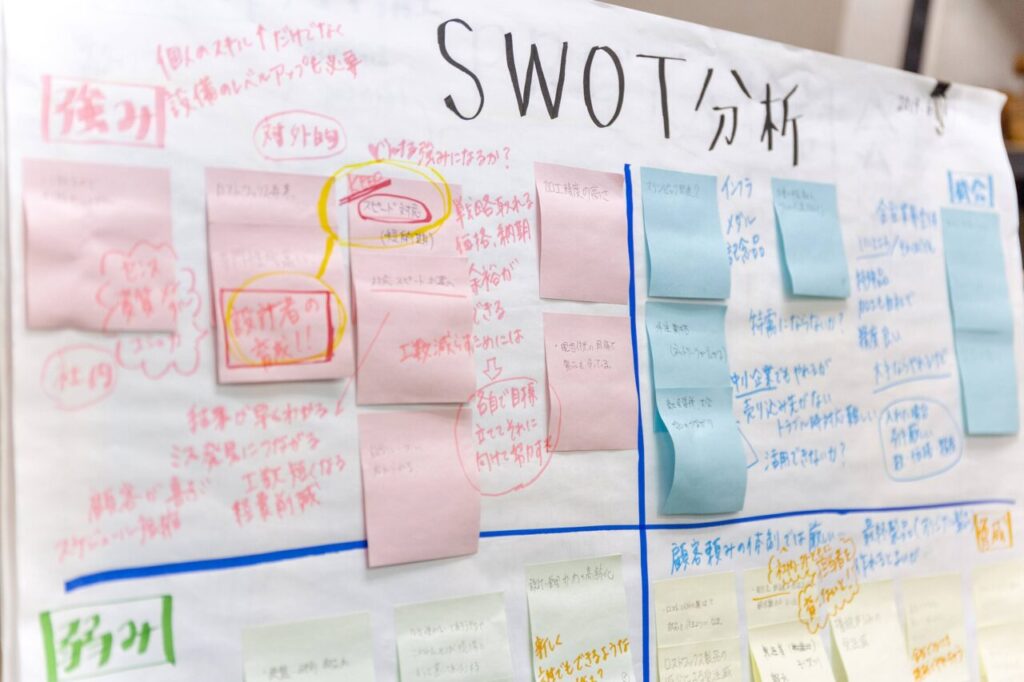
強み、弱み、機会、脅威を把握、分析する「SWOT分析」で、今後の戦略や課題を明確にする
モノづくりの技術と楽しさを継承するインターンシップ
2018年頃からはインターンシップを行っています。通常インターンシップには、入社してもらうことを目的にしたものと、職業体験のための2種類があると思いますが、うちは後者です。
参加する若者も、仕事内容に興味がある方と、とりあえず来たという感じの方に分かれます。作業は1日や2日でできるようになるわけではないので、内容を絞るのが難しいのですが、「金型とは何か」を説明しても伝わりづらいので、実際に加工することで、少しでも実感してもらえればいいなと思っています。
昨今では金型について知らない人も多いのですが、世の中で量産される製品の大半は、金型で造られています。日本の製造業の根幹ともいえる、この技術を継承したいという思いが私たちにはあります。
インターンシップで「楽しい」という感想を聞くと、教え甲斐がありますね。その楽しかった体験を次に繋げるためにはどうすればいいのかと、知恵を絞っているところです。
自分たちと協力会社さんで成り立っている小さな会社なので、発信力は弱いと思います。だからすぐに成果が出なくても、1人でも多くの人に体験してもらい、「まずはうちのことを知ってもらえたら」と思っています。それに、若い人の中にもモノづくりが好きだという子はいます。体験して、うちに入社しなかったとしても、その若者が将来モノづくりに携わってくれたら嬉しいですね。
今後はより詳細なコンピューターの使い方や、加工だけでなく組み付けの体験もやっていきたいと思います。インターンシップの様子はYouTubeにもアップしています。インターンシップでのノウハウは新人研修にも使えるという発見も、自分たちにとって収穫でした。
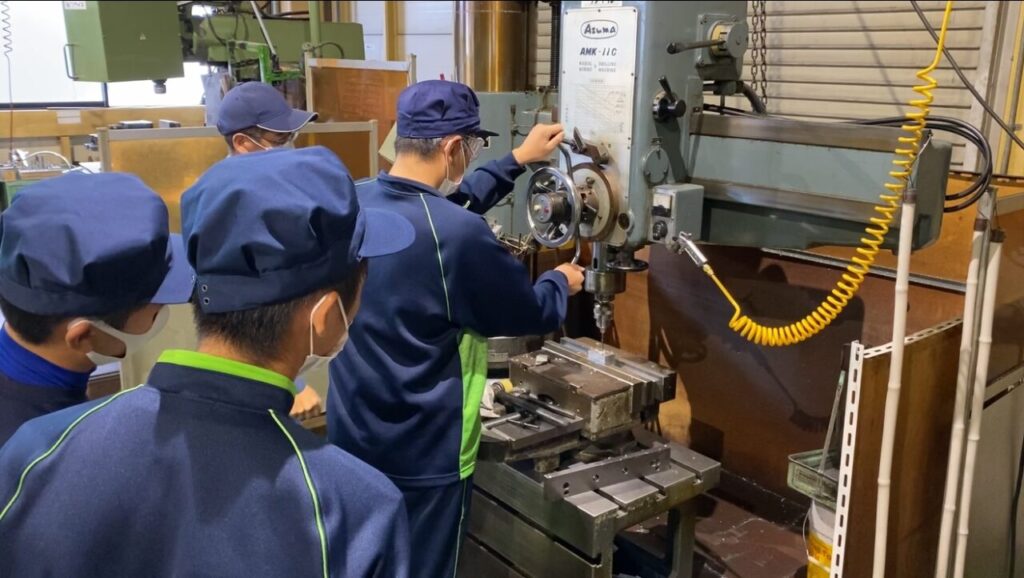
高校生によるインターンシップの様子
造仏方法から着想を得て、現会長が創業
ダイキ精工の設立は 1973(昭和48)年、創業者は会長である父の大迫喜一郎です。父は福岡県の工業高校を卒業し、機械加工や金型製造などの会社をいくつか渡り歩いた後、千葉県のマグネット製造会社へ。硬い材質で造るマグネットはダイアモンドでしか削れませんが、その方法では費用が掛かります。ほかの方法を模索した際、奈良の大仏を作る際にも使われた、粘土とロウを使った「ろう型鋳造」の方法に着想を得て、ロストワックス製法に辿り着きました。
そこで技術を身につけて、母と共に東京で独立。しかし、当時は終戦後で、工作機械の仕事の変動が激しかったため、経営は苦しかったそうです。
知人から「愛知でロストワックス製法による編み機の部品の需要がある」と聞き、愛知県へ。小牧市で50坪の工場でスタートしました。その後はアメリカのロストワックスメーカーへ製法を習いに行くなどして知見を増やし、オイルショックや大手商社との取引なども経験しました。
2012(平成24)年に代表取締役を交代しましたが、86歳の現在も現役です。朝8時に出社してラジオ体操をしてから、「技術屋が一度手を止めると、頭の切り替えが大変だから」と、私たちの代わりに銀行の人や飛び込み営業の人に対応してくれています。
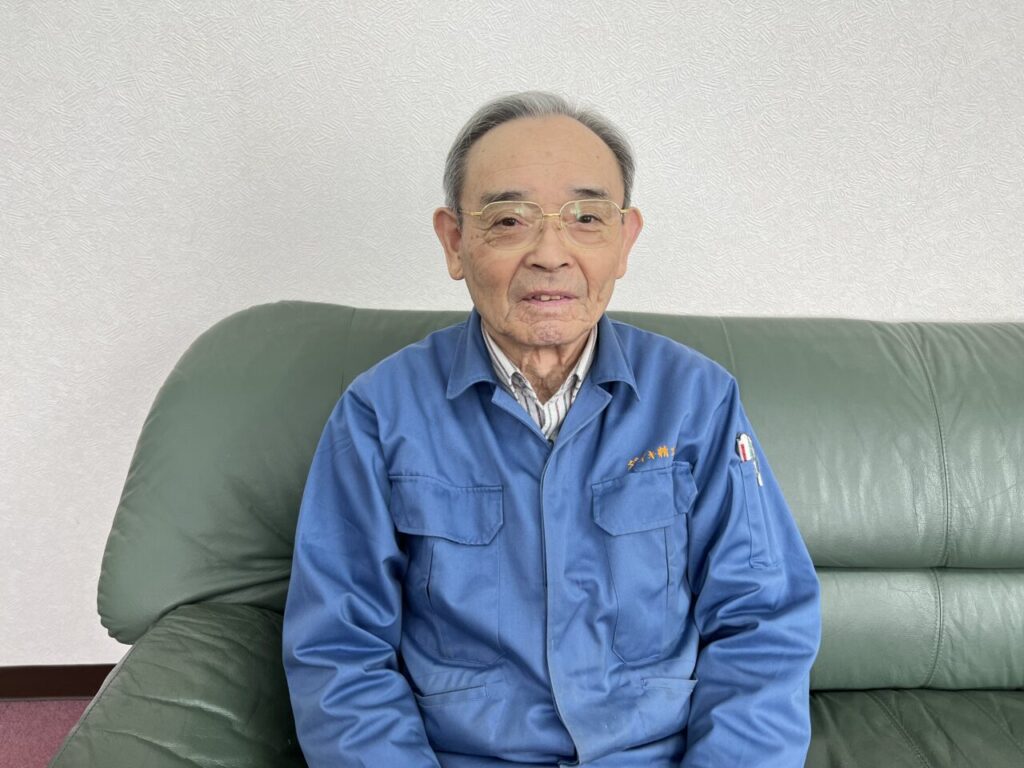
矍鑠(かくしゃく)とした大迫喜一郎会長は昭和11年生まれ。 「若い頃から仕事が好き。社長(宏和氏)がうちに来てくれて、非常に助かりました」と話す
「困っている人を助ける」という気持ちで作業
私もこの業界では素人でした。元々はSEとして、別の会社で10年ほど働いていたんです。いずれは妻(大迫会長の娘である早苗氏)と共に、自分の地元に帰って独立しようと思っていた時、会長から声がかかり、修行のつもりでダイキ精工に入りました。
それまでSEとしてパソコンと向き合ってきて、モノの現物に触れていなかったので、旋盤を使ってモノを削ると形になり、製品ができるということに、ものづくりの喜びを覚えました。思い返せば、少年期はプラモデル作りに没頭していましたし、図形も好きでした。
そして、リーマンショックなど様々なできごとを経て、会長から「君は現場をわかっているし、全体を見られる。ダイキ精工を継いでくれないか」と言われました。自分でも、一から会社を立ち上げることが大変だとわかっていたので、そう言っていただけたことに感謝し、お引き受けしました。従業員も「齋藤さんなら」と言ってくれ、嬉しかったですね。
現場で旋盤の仕事からはじめる中、「次の人が使いやすいように」、「困っている人を助けられる仕事を」と、思いやりを持ちながら作業してきました。お客さまが一番大切だという気持ちは、当時から変わりません。
大変なことは、常に技術が進歩し、求められる製品の精度も高くなることです。図面を鉛筆で書いていた時代もありましたが、今はコンピューターやCAD/CAMを使い、旋盤やフライスは自動制御のマシニングセンタへ。加工機も3軸から5軸へと進化しました。
世の中がより便利で快適になり、多種多様なニーズが生まれています。そういった時代の転換に応じて、必要とされる金型も、より複雑な形状のものへと変わっています。
職人魂を込めたアルミ風鈴の音色と共に、未来へ一手
コロナ禍で金型の受注がなくなった時、「金型の認知に繋がるような自社製品を造ろう」と考えました。金型鋳造業界は、年間を通して受注が一定ではないので、仕事がない時に自社で造るものがあるといいなという思いもありました。ある時ニュースを見たら、テレビに南部鉄器の風鈴が映っていました。うちの金型はアルミが大半で、工場内には端材があります。「この端材で風鈴を作ってみたらどんな音がするだろう」と思いついて、削ってみたら、澄んだ美しい音がしました。そこで、人々の気持ちが和むような音を奏でる、アルミの風鈴を造ろうと考えたのです。
最初はノーマルな形から始めたのですが、従業員に声をかけて、「風鈴選手権」を開催することに。各自が風鈴をデザインして削り、きれいな音が出るように試作しました。少し厚みが違うと音色が変わり、形にこだわりすぎるといい音が出ないことがわかって、試行錯誤を繰り返しました。
「思ったような音が出ない!」「文字を彫り入れたデザインもいいのでは」などと意見が飛び交い、みんなの職人魂に火がついたようです。
1つ1つ職人が削っているので手間が掛かっています。ガラスの風鈴では割れやすいし、鉄は錆びるという弱点がありますが、アルミの風鈴であれば軽くて丈夫で、お子さんにも楽しんでいただけることが自慢です。マンションなどの住宅事情に配慮して、室内でも楽しめる風鈴スタンドも作っています。
社内で盛り上がるだけでなく、小牧市役所やこまき新産業振興センターの方にも声をかけさせていただいたことで、ふるさと納税の返礼品にも選ばれました。
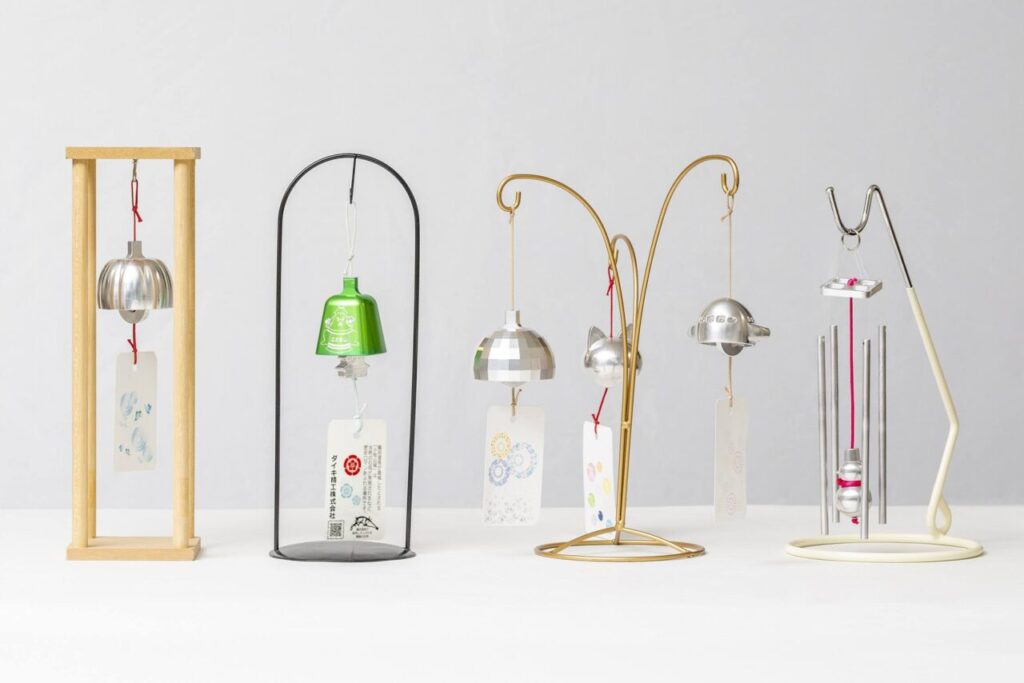
左からアルミ風鈴「凪」、「こまき山」、「煌」、「ねこ」、「飛行機」、「スノーマン」。アルミ風鈴は5000円〜8000円で、ホームページから購入可能
ご購入者さまからは、「音が良い」「きらきら光ってきれい」と褒めていただいています。現在はネット販売がメインで、あくまで会社のPR用として製作していますが、表に出せない顧客の金型と違い、自社製品として技術やアイデアを形にして、リアルの場に持っていけるモノができた意味は大きいですね。
そして、「自分たちはお客さまに喜ばれるモノを作っている。いい仕事をしているんだな」と、従業員に実感してもらえたことがよかったと思います。
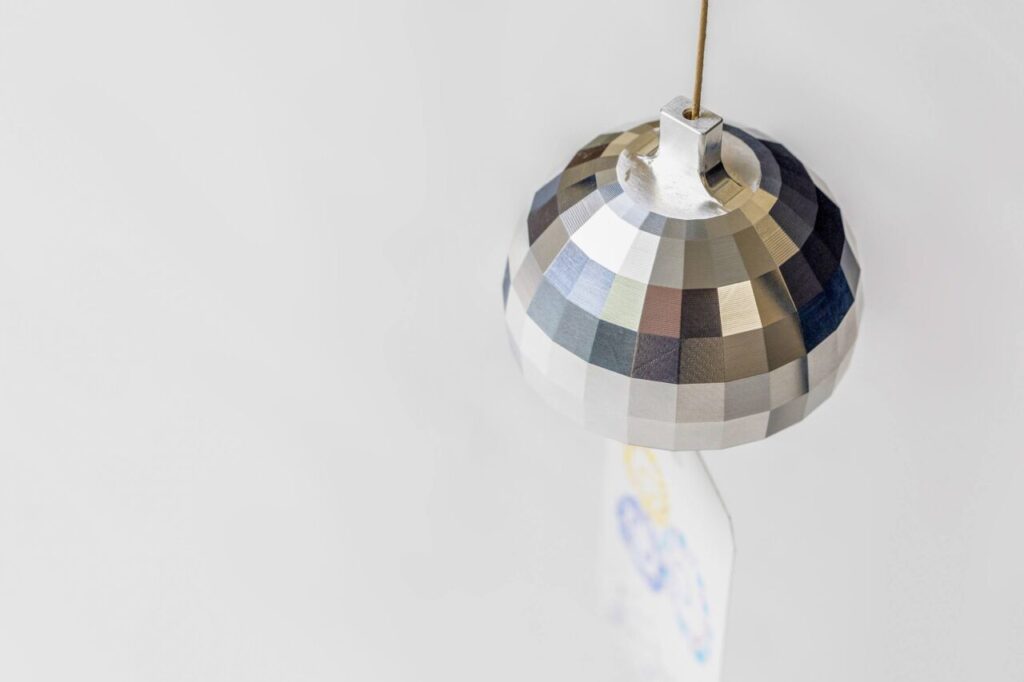
一番人気の「煌(こう)」は美しい音色と職人の技が堪能できる
製造業に携わる者として、今後は脱炭素についても考えていかなければならないと思います。現在は100年に一度の転換期。エネルギーの変化や電気自動車へのシフトによって、部品点数が減って、金型の需要も減るかもしれません。これからのことは未知数ですが、いかに時代のニーズを掴みながら、新しい分野で頑張っていけるかが鍵になるでしょう。
私たちは、このままロストワックス製法で進んでいくと思います。環境にフレキシブルに対応するために、組織は軽くしていたいですね。モノづくりの技術を継承しつつ、今いる従業員の力量をアップしていきたい。そして若い人を含めて、みんなに「仕事って楽しい」「モノづくりって面白い」と思ってもらえるよう、魅力的な会社でいたいと思っています。
会社所在地
〒485-0827 愛知県小牧市文津天王塚642-2
TEL(0568)-72-8660 FAX(0568)-72-8065
E-Mail:info@daiki-seiko.co.jp
Webサイト URL
代表者
代表取締役社長 齋藤宏和
事業内容
ロストワックス用精密金型の設計・製作。各種部品加工、治具製作。
【資本金】
1,000 万円
コメント